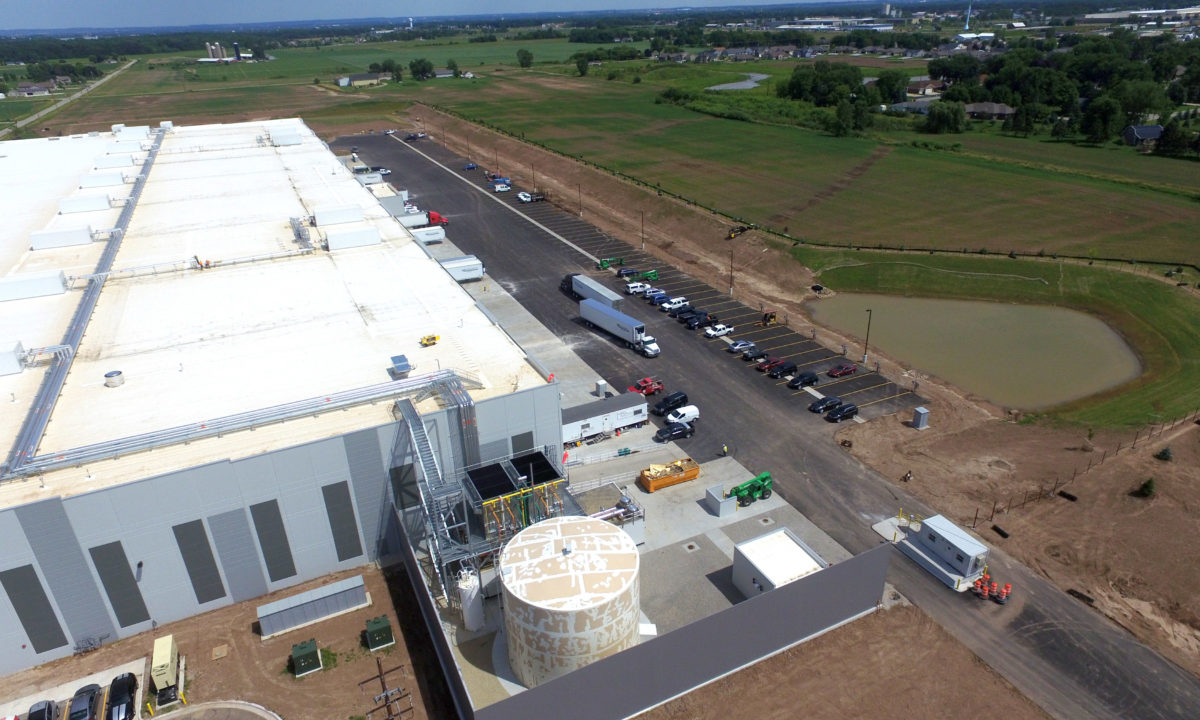
Engineering the Redistribution Center
Innovative was proud to provide our client with refrigeration for its new Redistribution Center that’s been up and running for more than a year. Their new 275,000 square-foot storage facility operates at -15℉ and runs on only a 6,000-pound charge of ammonia.
The project came to Innovative in November 2016. We worked with contractor FCL Builders, developer Scannell Properties, and GMA Architects.
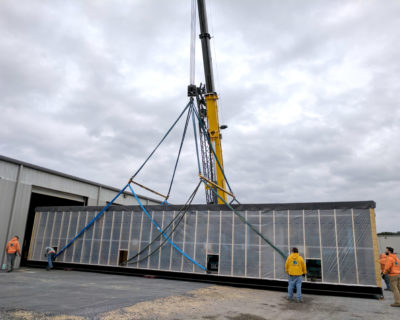
Typically, a recirculated ammonia refrigeration facility like this would have about 20-25 pounds of ammonia per ton of refrigeration. For this project, Innovative installed approximately seven pounds per ton, thanks to the low-charge design developed by our incredible engineering department. We did this by utilizing custom direct expansion evaporators, eliminating a high-pressure receiver, and replacing the thermosyphon oil cooling with glycol circulated through the same evaporative condenser that cools the ammonia. Direct expansion isn’t a new technology in the refrigeration world, but our engineers came up with a new, Innovative take on it, further reducing the overall charge!
Up top, Innovative used its mini-penthouse design, with some modification — we used modulating control valves with a PID loop for super heat/quality control of each evaporator. Despite the added challenge of working on a design it hadn’t seen before, our manufacturing team did an amazing job completing the project ahead of schedule. We found great success throughout the entire project, and that begins with our engineering and manufacturing teams.
The schedule was fast-paced. Building in Wisconsin in the winter provided the added environmental challenges of snow and low temperatures. Our team members blazed through the cold to finish the job only four and a half months from when we arrived on site in mid-February. FCL Builders, the GC, was a great help in this. Despite multiple weather delays, they were able to coordinate a few key trades to meet our overall project goals in a timely manner. They were professional, on task, and instrumental in keeping the project on track.
Inside, the freezer temperatures are -15℉ or colder, and the dock operates at 30 degrees. We were able to employ reheat on the dock via an underfloor heating system utilizing waste heat, which allowed us to keep the floors dry and the humidity in check.
The 6.3 acres of freezing space has 102,000 linear feet of glycol tubing. That’s 19.3 miles of tubing, used to prevent the actual ground underneath the building from freezing!
The project has a doublewide prefabricated mechanical house and an extensive steel structure that includes a condenser platform and a staircase up to the roof. This was a major engineering accomplishment! Our field team did a great job setting the house, erecting the platform, and installing two evaporative condensers — all in one day.
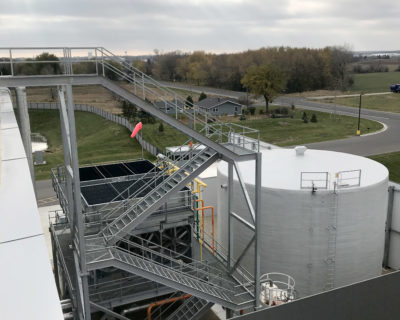
Innovative also installed 33 additional temperature sensors that were broken up into stacks and strategically placed across the warehouse. These eleven locations included high, medium, and low elevations. These extra sensors, which are in addition to the return air sensors at each penthouse unit, ensure that the facility temperature is always within two degrees of the control point.
The facility also has an HMI system and Innovative’s trademark ePSM product for process safety management.
Our team members always enjoy working with large, global brands like this one, which will use the new plant as a pizza redistribution center.
We are just wrapping up the first year of a 10-year warranty. Our maintenance agreement offers a bumper-to-bumper warranty on the project. We look forward to our facility providing a home for the client for many years to come!