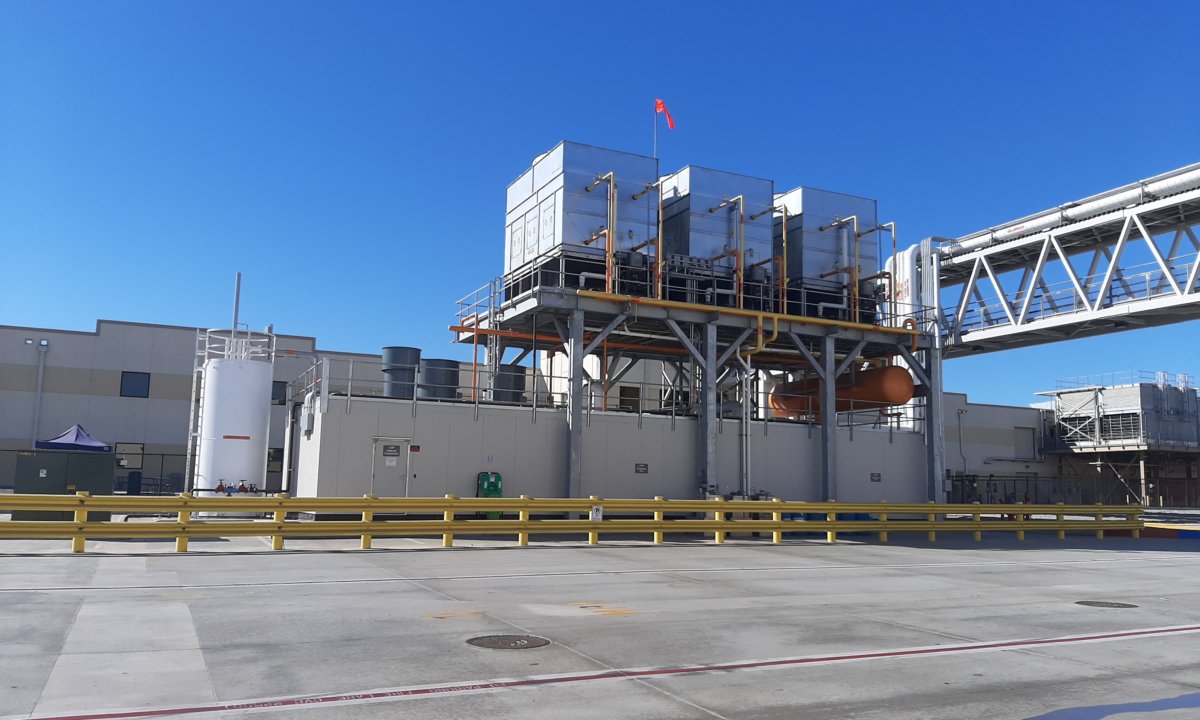
Industry Today: Prefabrication at Innovative
Innovative Refrigeration Systems provides single-source design, fabrication, and installation of customized turnkey industrial refrigeration
Innovative’s latest development are prefabricated mechanical enclosures they deliver to customer facilities – and even their rooftops, with the help of its Combilift System, capable of lifting 96,000 pounds over 16 feet high. These can be built and delivered in roughly 12 weeks.
John Stoklosa, VP of Engineering explains, “These are skid-mounted, fully-lit and fully insulated enclosures with removable walls and roof. It contains the ‘brains’ of an industrial refrigeration system—all the operating components including the full set of controls. Our standard package can interface with separate evaporators. The Master Series offers more flexibility with customization to house evaporators and compressors in one package.”
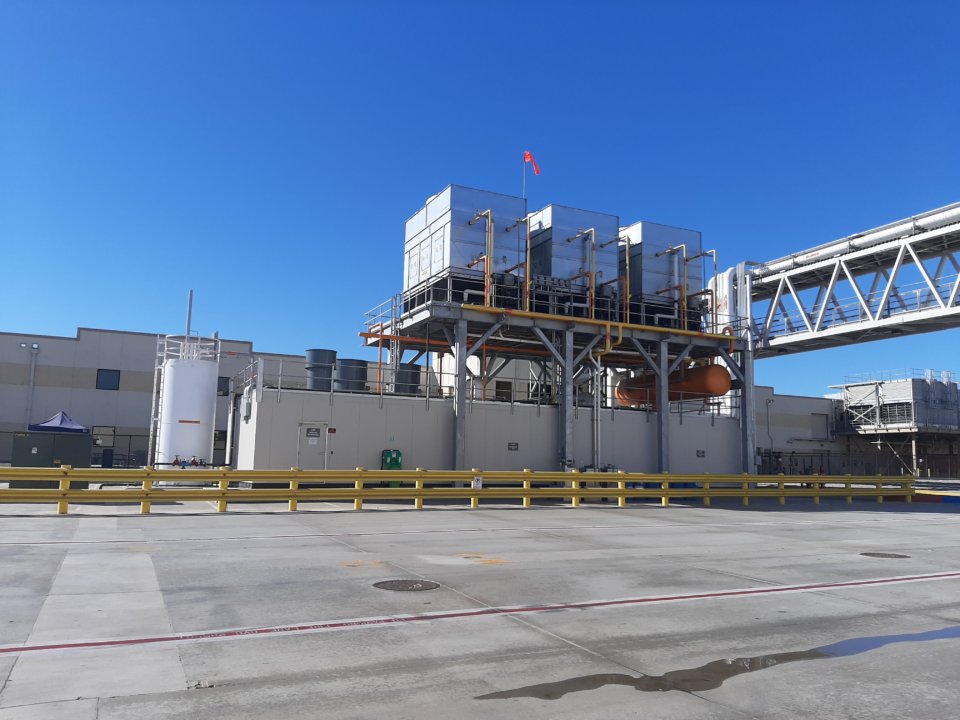
Once the customer facility has poured a concrete slab and it has cured, in less than a day Innovative can fully assemble the refrigeration system in place.
Innovative also has roof mounted mini-penthouse air handling units that can be seismic and/or hurricane rated. These units typically contain the following features:
- Access doors
- Interior grating
- Partitions
- Ammonia detectors
- Insulation
- Temperature probes
- Lighting
- Stainless steel piping
- Galvanized steel drain lines
Prefabricated Advantages
The comprehensive approach to industrial refrigeration that Innovative champions is taken a step further by building all of of these prefabricated units in-house.
Owner Mike McGinnis talks about the advantages gained here:
“There are a lot of advantages to prefab construction. It’s built faster, for one thing. You don’t have to dispatch crews to a construction site that gets disrupted by weather, you don’t have to deal with contractors not showing up when they are supposed to or system parts not arriving at time. There is better quality control and system reliability because everything is constructed under one roof by a dedicated team in a climate-controlled environment. All of which contributes to significant costs savings of prefab compared to on-site construction.”
Additionally, a prefabricated structure like Innovative’s provide a greater safety factor. One example being that mini-penthouses only require a four-foot at most to reach anything within the structure due to its design. This reduces the risk for falls and the need to reach for objects that are not necessarily within reach.
Growing Demand
Nearly 30 years ago, roughly 5% of Innovative’s business came from prefabricated unit manufacturing. Over the last three decades, the demand has rise and now constitutes 65-70% of Innovative’s capacity for business. This had led to some notable expansions within the company, specifically the addition of 40,000+ Sq. Ft. in shop space, totaling 182,951 Sq. Ft. in office and shop space at Innovative.
While other companies attempt to carry out prefabrication initiatives, many of these companies outsource this execution to a third party. Innovative sets themselves apart by being able to complete each project in-house.
Mike McGinnis explains this below:
“We’ve been offering full-service, in-house design and engineering, manufacturing, construction, project management and aftermarket support performed by experiencing professionals since our inception. As design-build contractors, we’re fully competent in every step of the process which makes it easy for us to apply these same disciplines to build our prefabricated units.”