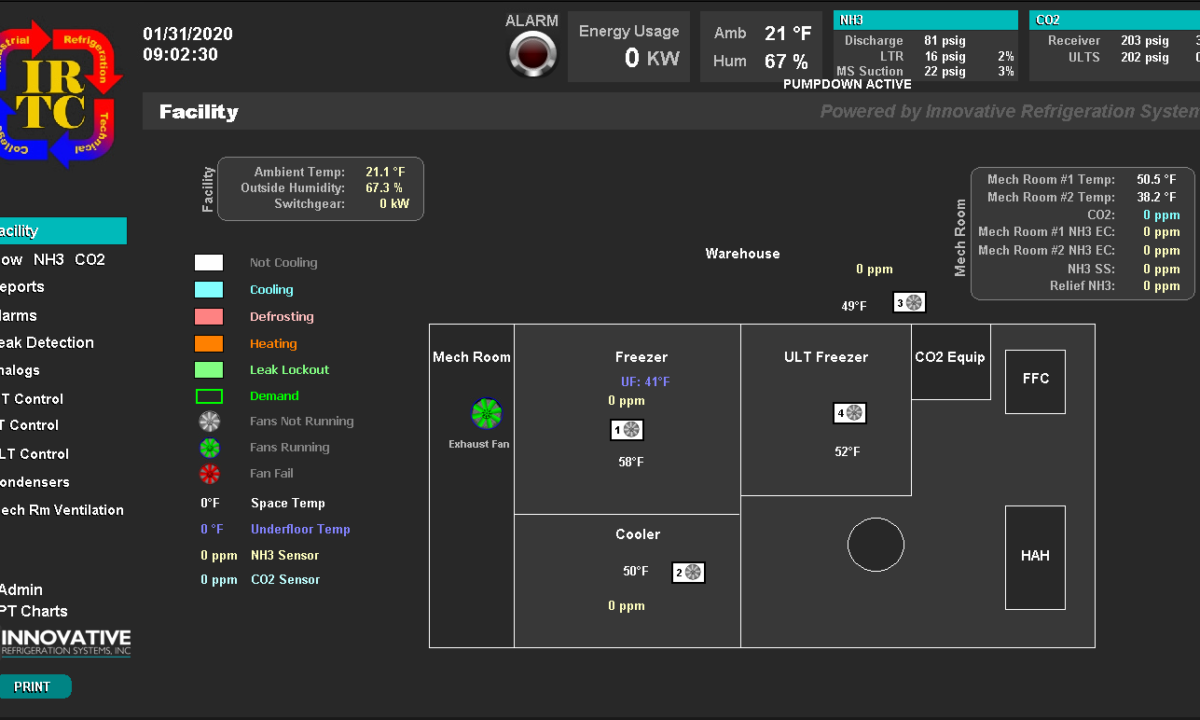
Why you should switch to a modern HMI
Early refrigeration/automation systems were run purely electro-mechanically. That is, the mechanical processes were controlled by electricity via pre-made circuits.
Making changes on these systems, such as changing the order in which compressors run, would require either rewiring the circuit, or having a complex circuit that would be very difficult to troubleshoot if something was not working properly.
The development of the Programmable Logic Controller (PLC) in the 1960s, allowed for these circuits to be greatly simplified, as most of the logic could instead be handled by the PLC.
Early PLCs could be controlled via an interface called a mimic panel. These panels consisted of buttons and switches (to control the equipment), coupled with a process flow diagram with LEDs and gauges (to indicate the status of the equipment).
Mimic panels could still be difficult to troubleshoot, as an operator would have to be present when an issue was occurring to determine its cause. Additionally, changes could only be made to the system by an operator who was physically in the room in which the panel was located.
An example mimic panel. An example mimic panel.
As computers became cheaper and more commonplace in the 1990s, the mimic panel interface began to be replaced by the Human Machine Interface (HMI).
These HMIs replaced the physical buttons and lights of the mimic panel with graphical representations on a computer screen. This typically resulted in simplified interfaces, which made it easier for non-technical users to change system set points.
The modern PLC-HMI is even further improved. Now, users can receive notifications about their system, can easily log operation trends, and can even remotely access the system.

In industrial refrigeration systems, a modern HMI can be beneficial in many ways. For example, an alert could be sent via email/text if the temperature in a room is too high or too low, or if a piece of equipment fails, or if there is a refrigerant leak. Receiving notifications immediately helps operators react to incidents faster, and helps facilities proactively resolve problems.
Using a modern PLC-HMI with an ammonia refrigeration system also allows real-time monitoring of performance from a remote location. In some cases, the system can even be controlled remotely; this is the technology that allows Innovative Refrigeration Systems to remotely troubleshoot systems for clients who have a service plan.
The ability to log system data helps tremendously with troubleshooting. Being able to check the logged data and events can help immensely when trying to troubleshoot issues: rather than checking wires and trying to re-create conditions, one can simply look at the logged events before and after a problem occurred.
Being able to log system data is also advantageous for record-keeping/compliance purposes. With room temperatures being logged constantly, there’s no longer the need for an employee to record it manually. This also gives facilities the ability to adjust equipment based on historical data, potentially catching a compliance issue before it occurs.
Modern PLC-HMIs, such as the ones that Innovative Refrigeration Systems installs for its ammonia refrigeration customers, can help prevent issues and help troubleshoot them when they do arise.