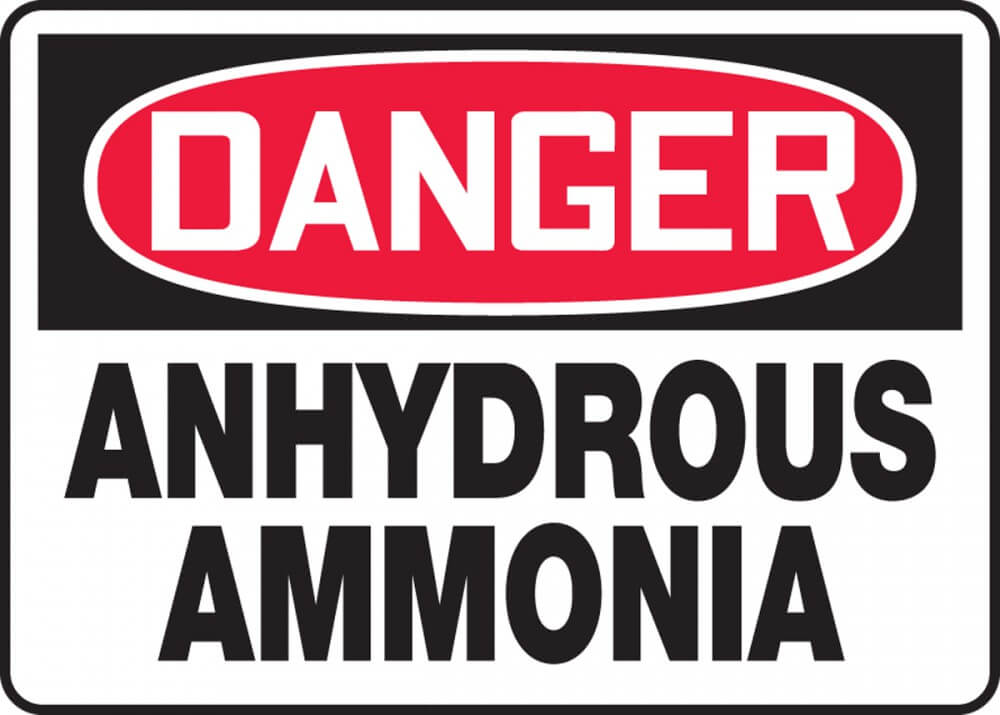
How to Work with Ammonia Safely

Ammonia is classified by OSHA as a hazardous chemical. While ammonia leaks are rare when following proper procedures, they can still occur. The most common symptoms experienced as a result of an ammonia leak are skin and eye irritation, respiratory irritation, and coughing. Most ammonia leaks are small and do not pose serious health risks. This is in part thanks to ammonia’s self-alarming nature. Unlike other refrigerants, ammonia has a strong odor that can be detected well before the concentration becomes dangerous. In fact, humans can smell ammonia leaks sooner than many alarm systems can detect a leak. Despite ammonia’s self-alarming properties, it is still critical to take proper precautions to prevent a leak, and have proper training in place in the event a leak does occur.
1. Have a Well-Designed Infrastructure
A well-engineered infrastructure should come standard with any ammonia system and will help prevent and control leaks. This infrastructure includes exhaust fans and dispersion tanks, to direct the flow of ammonia away from your workers in the case of a leak. Thanks to ammonia’s eco-friendly nature, exhaust fans can vent into the open air and away from workers if a leak occurs.
Designing with risk management in mind will help prevent leaks in the first place. For example, using rooftop penthouse evaporator units instead of regular indoor evaporator units eliminates the risk of employees damaging the evaporators with forklifts and other equipment. Damage to the evaporators could cause a leak, so penthouse units are a safer option. Another way to improve safety is to keep your ammonia charge under 10,000lbs. When you keep the charge less than 10,000lbs, you take on less risk according to OSHA. OSHA’s PSM regulations won’t apply to you, because you are lowering your risk simply by keeping low levels of ammonia, however it is best to implement a RSM (Refrigeration Safety Management) plan to ensure you protect your employees.
2. Properly Train Your Employees
It is critical to provide basic awareness training to all employees that will be near ammonia systems. A well-trained staff that understands the risks associated with ammonia will greatly minimize any risk. Employees should also have HAZWOPER (Hazardous Waste Operations and Emergency Response) and ammonia first aid knowledge included in their training. Beyond basic training, operators should receive additional training in the form of certifications from the Refrigerating Engineers & Technicians Association (RETA). Classes can be taken online for this training, but a hands-on training program such as Innovative’s Industrial Refrigeration Technical College (IRTC) enables trainees to perform safety procedures in a real world refrigeration environment.
3. Properly Maintain the System
Proper maintenance of an ammonia system will ensure that the infrastructure remains durable and efficient, reducing the risk of leaks and other accidents. If your system is subject to PSM regulations, the required maintenance and file keeping will be clearly outlined. Utilizing an electronic PSM platform such as Innovative’s ePSM software can simplify your compliance program even further, and save time and money on burdensome paperwork. Even if you don’t fall under PSM regulations, the International Institute of Ammonia Refrigeration (IIAR) covers the inspections that need to be performed. Additionally, a strong Preventative Maintenance (PM) plan will keep ammonia systems running longer and reduce the odds of costly repairs and replacements.
Review
Ammonia is a potentially dangerous substance, but a well-thought-out plan will drastically reduce risk. In modern systems, ammonia leaks are improbable, and when they do occur, risk can be minimized with a properly implemented safety and training program. Proper design, training, and service/maintenance will create a safer work environment.